Saturday was the day to see whether the factory laid-up engine pan was to make it into the boat build. I started by securing a length of string (plumb-bob string mind you, this is hi-tech stuff!), centered in the shaft log. The string represents the center line of the propeller shaft, and serves as the reference point from which ostensibly the engine is built around. But to build an engine around this datum, it is first necessary to install an engine bed to accept the engine. In this case, I was going for the installation of a nice, factory laid-up engine pan (complete with gelcoat).
As you can see, the string is following the center of the shaft log as it is extended into the engine room. The string was pulled tight, and clamped to the forward portion of the engine pan.
With the string, representing the propeller shaft, pulled tight and secured in its proper plane and positioning, I lowered the B-38 template I recently crafted into position. With some cajoling of the template and use of some scrap wood, I was able to align the template in the same plane of the string.
As can be seen below, the string intersects the aft portion of the engine template precisely in the position intended - at the gearbox output / shaft coupling - 3.1" below the bottom of the template.
Ensuring that the engine shared the string's (propeller shaft's) plane, the forward portion of the engine template also intersected the string at 3.1" below the engine template - in this case, the bottom of the engine template represents the bottom of the engine feet.
So with the engine template in position, it was time to talk myself into making this W32 engine pan work in the boat build. To begin with , I looked over the port side of the template. In the picture below, the immediate issue of the location of the port aft engine motor mount - represented here by pictured block of wood. The engine feet have a width dimension at the base of roughly 2.5". So the first issue is the port side's aft motor mount base interfering with the outboard side of the engine pan.
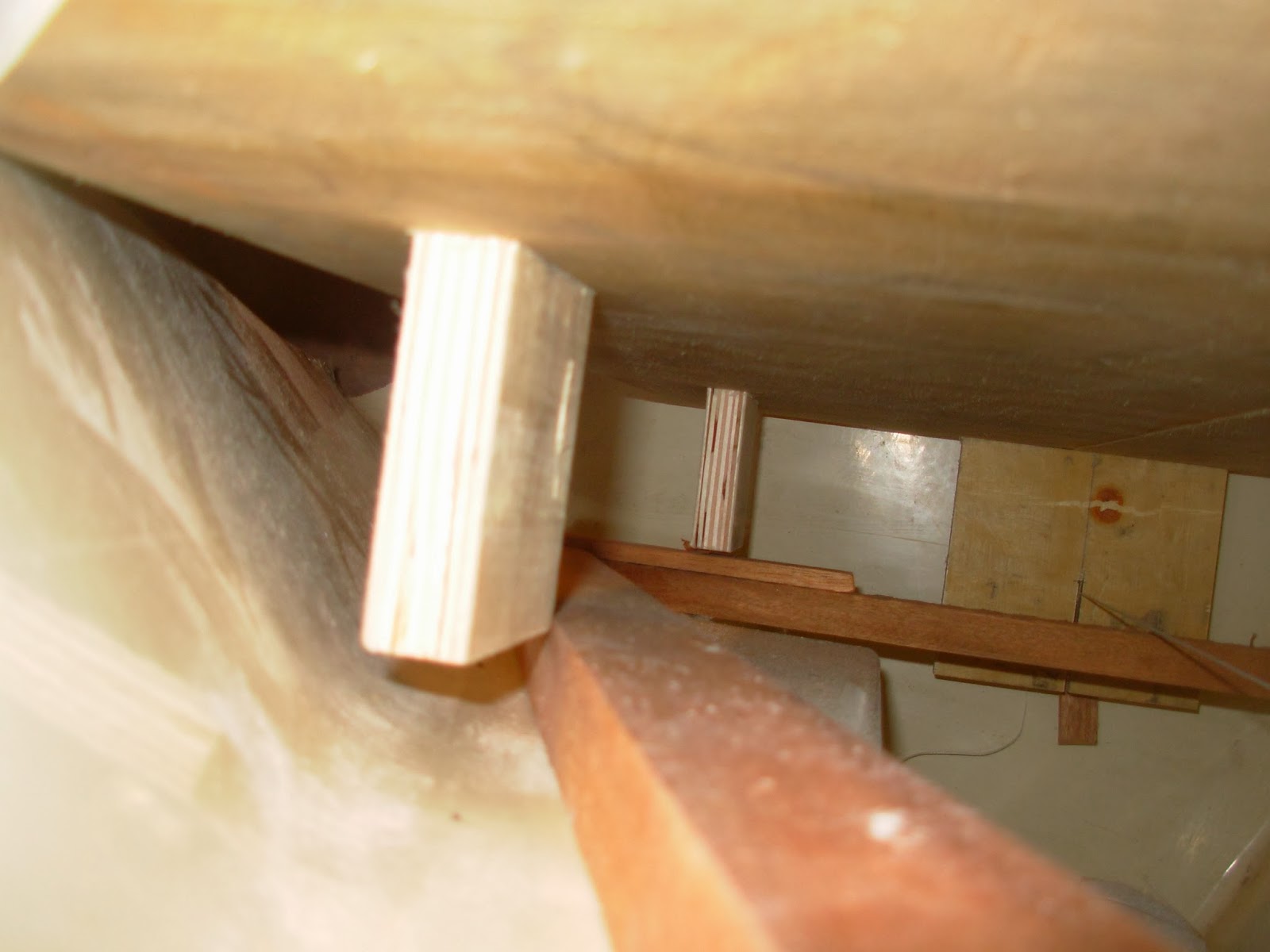
Moving to the port side's forward engine motor mount, the problem is obvious. The engine for which this pan was originally designed for - the Volvo MD-17, or similar from the '70s - has a wider dimension. The Beta-38, although holding more horsepower, has a smaller plant dimension, and is more narrow at the forward end. As a result of the narrow width the B-38, the motor mounts ended up well-inside the engine pan's bearing surface. If this pan was to be used, I would need to accommodate this void, and fabricate an extension of the pan's bearing surface to accept the forward motor mount.
Here is another shot of the port side's forward motor mount position, showing it falling inside of the more desired location.
Turning to the starboard side's aft motor mount position, the location here, like that of the port side, is too far outboard. Again the base of the motor mount could not be seated properly due to the engine pan's outboard surface.
The starboard side's forward motor mount can be clearly see to be too far inboard, missing the pan's engine bearing surface - similar to the port side.
Here is another shot of the starboard side's forward motor mount (again, represented by the wood block in vertical alignment to that of the template), missing the engine pan's bearing surface. With many of the questions I had now being answered by the alignment of the B-38 template over the engine pan, I had satisfied my curiosity and resigned to the decision to start fresh and build an engine bed customized to the B-38. Agonizing over this decision was eliminated after further consultation with a friend and experienced builder. The engine installation is still a ways out, so the B-38 may not ultimately be the engine that I install, or dimensions may change. For now, however, the engine pan will be a no-go.
Total Time: 2 Hrs.